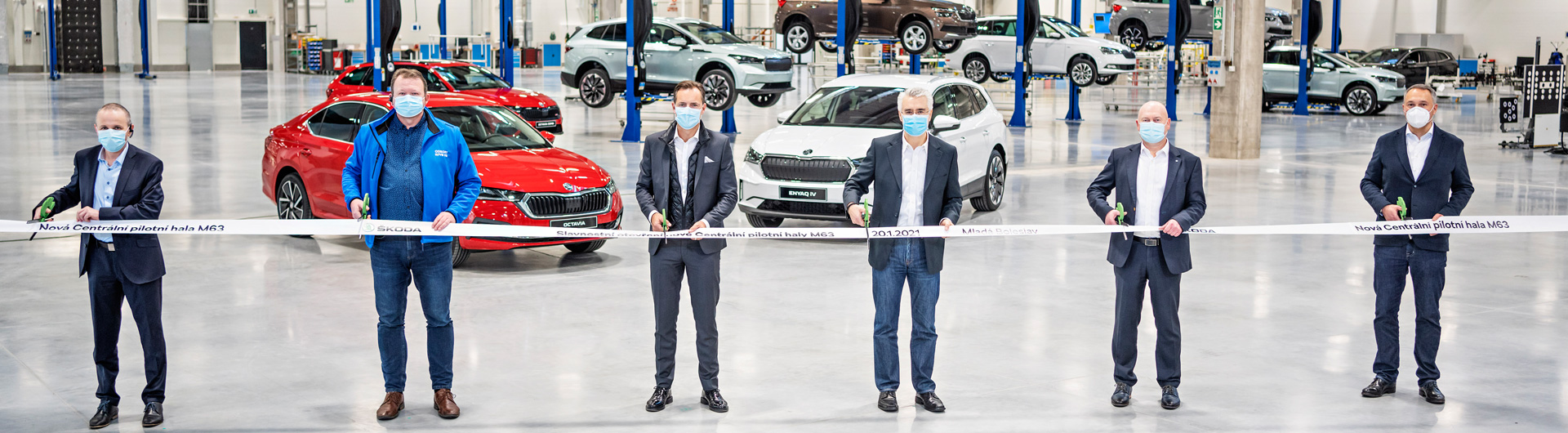
KODA uroczyście otworzyła nowoczesne centrum pojazdów testowych i prototypów
KODA uroczyście otworzyła nowoczesne centrum pojazdów testowych i prototypów
W nowym centrum produkcji pojazdów testowych i prototypowych KODY zastosowano najnowocześniejsze rozwiązania technologiczne. Stacje robotów, dobrze rozplanowana przestrzeń i rozwiązania z zakresu wirtualnej rzeczywistości pozwolą na budowanie 300 pojazdów testowych i 120 pojazdów prototypowych rocznie. Inwestycja, na którą składają się pomieszczenia o powierzchni ponad 12 000 m² wyniosła około 20,4 mln euro.
Dział Rozwoju Technicznego KODA AUTO otworzył w Mladá Boleslav nowe centrum produkcji pojazdów testowych i prototypowych. Oznacza to, że wszystkie te specjalne pojazdy można teraz budować pod jednym dachem. W całym procesie produkcyjnym marka wykorzystuje najnowocześniejsze technologie, takie jak stacje robotów i rozwiązania z zakresu wirtualnej rzeczywistości.
Rozwój pojazdów na najwyższym poziomie
– Korzystanie z samochodów testowych pozwala na wyciąganie wniosków na temat wielu parametrów technicznych na wczesnym etapie rozwoju pojazdu oraz dokonywanie niezbędnych korekt na długo przed rozpoczęciem seryjnej produkcji nowego modelu. Teraz robimy następny krok w tym kierunku. W przyszłości będziemy budować 300 pojazdów testowych i 120 prototypów rocznie pod jednym dachem w naszym najnowocześniejszym centrum w Mladá Boleslav. Stworzyliśmy tutaj idealne warunki do rozwoju pojazdów na najwyższym poziomie. Będzie to kształtować przyszłość naszej marki – mówi Johannes Neft, który 1 stycznia 2021 został nowym członkiem zarządu ds. rozwoju technicznego w KODA AUTO.
Choć cyfrowe symulacje i modele zyskują ostatnio na znaczeniu, to jednak klasyczne testy są niezbędne, by móc nie tylko monitorować poszczególne komponenty, ale również sprawdzać, jak pojazd działa jako całość. Ze względu na coraz bardziej złożoną i wydajną architekturę elektroniczną nowoczesnych pojazdów kładzie się duży nacisk na testy funkcjonalne elektryki, elektroniki i systemów wspomagających, a także na komunikację między komputerami samochodowymi. KODA wyprodukowała w nowej fabryce część pojazdów testowych dla elektrycznego SUV-a ENYAQ iV.
– Nasza nowa fabryka ma dwa piętra i mieści magazyn części, warsztat blacharski i lakiernię. Wszystko to rozmieszczone jest na niewielkiej powierzchni, co sprawia, że odległości między poszczególnymi działami są krótkie. Wysoki stopień automatyzacji zakładu pozwala na większą elastyczność procesów produkcyjnych i znaczny wzrost zdolności produkcyjnej pojazdów testowych i prototypów. Ponadto budynek wyposażony jest w najnowocześniejsze technologie z zakresu wirtualnej rzeczywistości, a także 168 miejsc pracy w biurach typu open space i 13 sal konferencyjnych. Duża część kompleksu jest wykorzystywana do produkcji pojazdów – dodaje David Vaněk, szef działu konstrukcji prototypów i modeli.
Robotyzacja, wirtualna rzeczywistość i najnowocześniejsze systemy informatyczne
Na parterze fabryki znajduje się magazyn części wraz z zadaszonym placem do rozładunku samochodów ciężarowych. Karoserie budowane są na pierwszym piętrze, natomiast na drugim piętrze odbywa się montaż końcowy i lakierowanie. Winda towarowa służy do transportu materiałów między piętrami.
Dzięki dwóm zrobotyzowanym stacjom udział automatyzacji w warsztacie blacharskim wzrósł z 15 do 45 procent. Podwaja to zdolność produkcyjną do dziesięciu karoserii tygodniowo, a jednocześnie zmniejsza wykorzystanie powierzchni budynku o 20 procent. Ponadto można tu również wytwarzać konstrukcje zmniejszające wagę pojazdu, ponieważ KODA rozszerzyła swój warsztat blacharski o centrum innowacji do testowania technik łączenia, takich jak łączenie klinowe, nitowanie, łączenie śrubowe (FDS), spawanie laserowe i konstrukcje kompozytowe.
Technologie z zakresu rzeczywistości wirtualnej umożliwiają wstępne konfigurowanie i dostosowywanie stacji roboczych, a w procesach logistycznych wykorzystywane są najnowocześniejsze systemy informatyczne. Kontrola jakości zostanie zintegrowana z procesem produkcyjnym i będzie prowadzona równolegle z poszczególnymi etapami produkcji. Nowy obiekt został wyposażony także w specjalne stanowisko pozwalające symulować jazdę testowanego samochodu z prędkością aż do 300 km/h.
W nowym centrum pojazdów testowych i prototypów zadbano również o ekologię. Krótkie odległości między poszczególnymi urządzeniami pozwalają zaoszczędzić około 1800 l paliwa rocznie, umożliwiając w ten sposób zmniejszenie emisji CO2 o około pięć ton. Połączenie magazynu z fabryką pojazdów skutkuje dalszymi oszczędnościami, zmniejszając koszty logistyki o ponad 150 000 euro rocznie.